Electrification
OEM’s make demands on suppliers for durable fastener sealant solutions to support EV market
Abstract
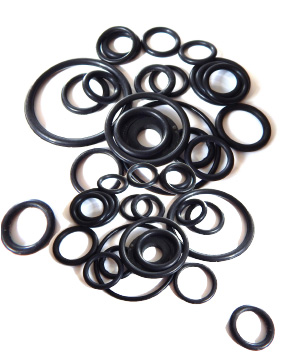
As electrification of vehicles becomes more mainstream, work is underway to address manufacturing issues unique to this technology. This includes mundane sounding, yet critical components such as fasteners. One specific challenge area has been to have a reliable, multiuse fastening system for enclosing battery cells into battery packs. Critically, no water can enter the enclosure, since significant thermal events can result if this occurs. Traditional fasteners with under head sealants require further development to provide dry, leak proof joints, even after repeated installations.
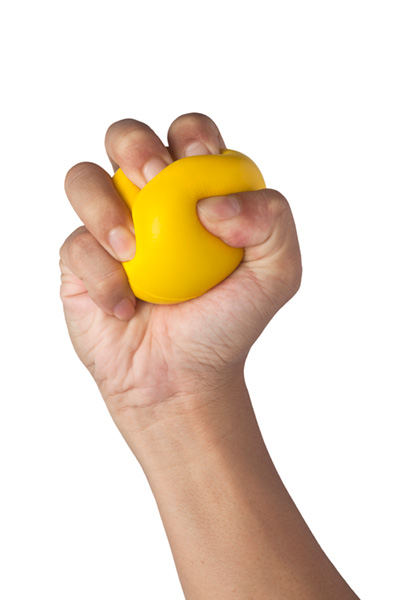
Introduction
Have you ever seen what happens when a soft sealant material, applied under the head of a bolt, is squeezed as the bolt gets tightened? Generally, the soft nature of the material, under such forces, causes material to squeeze out of the joint, thereby defeating its purpose. These soft materials are also often very poor in tear resistance, and high torsional forces exacerbate the issue. Typical hardness readings for these traditional sealants are around 50-55 on the Shore A Scale, soft enough to easily make an impression with light fingernail pressure. Often, after a single installation and removal, the under head sealant is torn, even mangled, and completely detached from the bearing surface of the bolt. In other words, the sealant and sealing function have been damaged. This presents a risky situation during vehicle service schedules, since mechanics often reuse the same fastener that was removed. In this mentioned case, the joint integrity is compromised. A better solution would be to use a fastener sealant that keeps its structural integrity after repeated uses.
O-rings are not always the solution. In fact, they have a variety of deficiencies on their own, including, but not limited to the following:
- No adherence to the fastener, allowing for slipping or rotation upon installation/removal/reinstallation
- Assembly required (O-rings on fasteners) which can be expensive and not always foolproof
- Multiple failure modes including improper sizing, over compression, damage on installation, spiral twisting failures, etc.
It is clear that, due to these limitations, a need exists for a more robust sealing solution.
Sealant hardness is very important for under head fastener sealing, and with the incredibly high installation forces (more extreme as the fastener size gets larger), there is an opportunity to increase robustness by using polymers that have relatively higher mechanical properties. Specifically, higher material hardness, and tensile strength are desired, while keeping a certain malleability of the sealant. In addition to hardness considerations, adhesion to the fastener surface is paramount. Strongly adhered sealants, combined with a formulation that has appropriate hardness for the application, provides a robust sealant solution. One such product on the market, Nylok’s NySeal® 2.0, has all of these characteristics, so much so that one major OEM has declared NySeal® 2.0 as a “best in class material” for under head sealing.
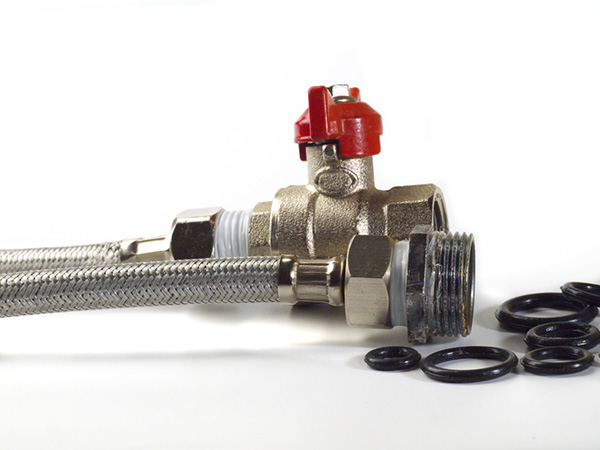
Sealing a lithium-ion battery cover for the ever-advancing electric vehicles takes on a new level of importance. If the right conditions exist, water can create a reaction with the lithium-ion battery generating explosive gases that can cause fires. Therefore, engineers at EV companies have shown great interest in upgrading to a sealant that holds its integrity after multiple installations. The risks are too high to rely on softer materials that don’t stay intact past the first installation.
For more information on Nylok® and NySeal® 2.0, please contact: sales@nylok.com.