Lightweighting Vehicles
How to Join Dissimilar Materials Using Steel Fasteners Without Galvanic Corrosion Effects
Abstract
Corporate Average Fuel Economy (CAFE) standards require that manufacturers of passenger cars and light trucks reach 41 miles/gallon average fuel economy by 2021. With that deadline fast approaching, there are still significant hurdles remaining, even with considerable progress made over past decades on engine optimization and vehicle electrification. One of the important enablers of complying with CAFE is to reduce the overall vehicle weight through the use of lightweight materials, such as magnesium, aluminum, and carbon fiber. Understanding the conditions needed for a galvanic cell to form is essential to solving the issue. Incredibly, there has been a limited amount of fastening techniques suitable for joining dissimilar materials in vehicles, even though the progress on lightweight design has proliferated. Recent new developments provide a pathway for compliance.
Introduction
“We’ve tried everything under the sun, and nothing solves this issue,” reported a senior corrosion expert at a leading OEM, when questioned about the best common practice(s) for joining parts made from dissimilar materials. After discussions with several such customers over this common market segment of automotive fastening, it became quite evident that galvanic corrosion issues for steel fasteners against dissimilar lightweight materials is a ubiquitous issue with no apparent suitable solution.
Automotive Scrutiny – Approving New Materials
Fastener and materials engineers at automotive OEM’s are relentless in their scrutiny of new coatings for vehicle applications, with good reason. Recently, the trend in automotive is for the life of the solution to match a 15 year vehicle life (up from 10 years). Materials used in engineered joints must pass rigorous testing, including temperature cycling, chemical resistance, creep resistance, and corrosion tests before and after high velocity impact testing with stones, among others. For fasteners, creep resistance is crucial, since a polymer that is applied on the bearing surface of the fastener is subjected to considerable compression forces. These can cause most polymers to creep or move over time, thereby creating a potentially unsafe loose joint condition.
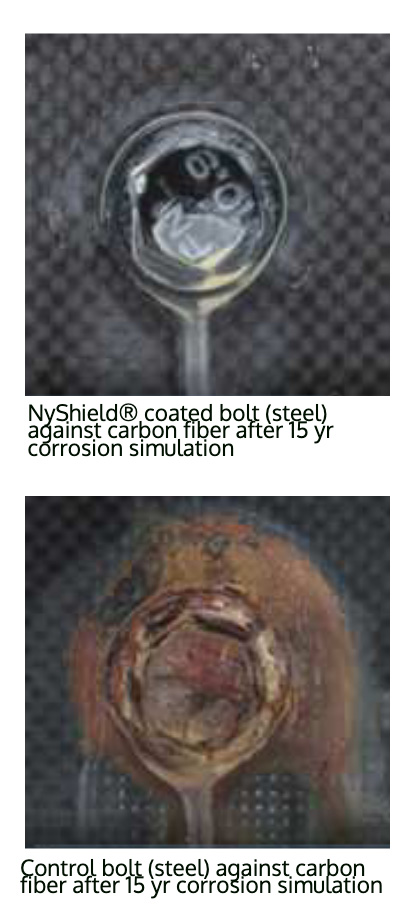
Fasteners, Substrates, Scope
One key difficulty in applying organic coating solutions onto fasteners is related to the fastener finish and topcoat. A mechanical zinc finish, for example, has relatively weak adhesion to the bolt surface, whereas electroplated zinc is strongly adhered. In the same way, topcoats are designed to offer advantages in lubricity, so that the fastener has a specific coefficient of friction range when driven. These “slippery” surfaces create difficulties for securely overlaying organic coatings. In providing value added organic coatings, the material selection has to perform well on key finishes/topcoats, and care must be taken to avoid known problematic material combinations.
Solution Space
NyShield® is a durable coating applied to fasteners that provides a barrier solution, allowing lightweight materials to be fastened without the occurrence of galvanic corrosion. This technology enables fastener engineers with the capability of using steel fasteners for joints that contain magnesium or carbon fiber, for example. Since there are only a few, bulky or expensive prior solutions, NyShield® offers a practical solution to a significant unmet customer need.
Clamp Load Loss
Since NyShield® is a thermosetting polymer, it has little mobility, on a molecular level, after it is cured. This is significant for an under head fastener application, since forces are extremely high. Most polymers cannot handle these high forces and squeeze out of the joint. NyShield® is effective in resisting these forces up to 125 degrees Celsius with no significant joint relaxation.
Electrical Isolation-Added Benefit
One prominent supplier of fastener solutions to electric vehicle OEM’s requested information on NyShield® related to its electrical resistivity. A third party conducted testing and revealed that the dielectric strength of the material was high. This fastener solutions company used NyShield® to isolate voltages on their fastener without using clumsy plastic sleeves. Since then, other electrical isolation applications have emerged, allowing for use of fasteners in places where electrical current containment was essential.
Conclusion
NyShield® offers an elegant and cost effective solution for attaching lightweight materials on vehicles for the purpose of meeting CAFE standards, without introducing galvanic corrosion effects. Not only does this coating provide the galvanic corrosion resistance needed to satisfy 15 year vehicle life requirements, it also is durable, creep resistant, chemically resistant, and has strong adhesion to steel substrates. An additional unintended benefit was also discovered; NyShield® has the ability to isolate electrical current in electric & hybrid vehicles, as well as in battery applications, thereby eliminating rudimentary work-around solutions.
For more information on Nylok® and NyShield®, please contact: sales@nylok.com.